In the world of non-destructive testing and preventative maintenance, thermographic inspection has emerged as a powerful tool. This cutting-edge technology harnesses the infrared spectrum to reveal hidden issues in various applications, from electrical systems to buildings. In this blog, we will explore the fascinating world of thermographic inspection and its myriad applications.
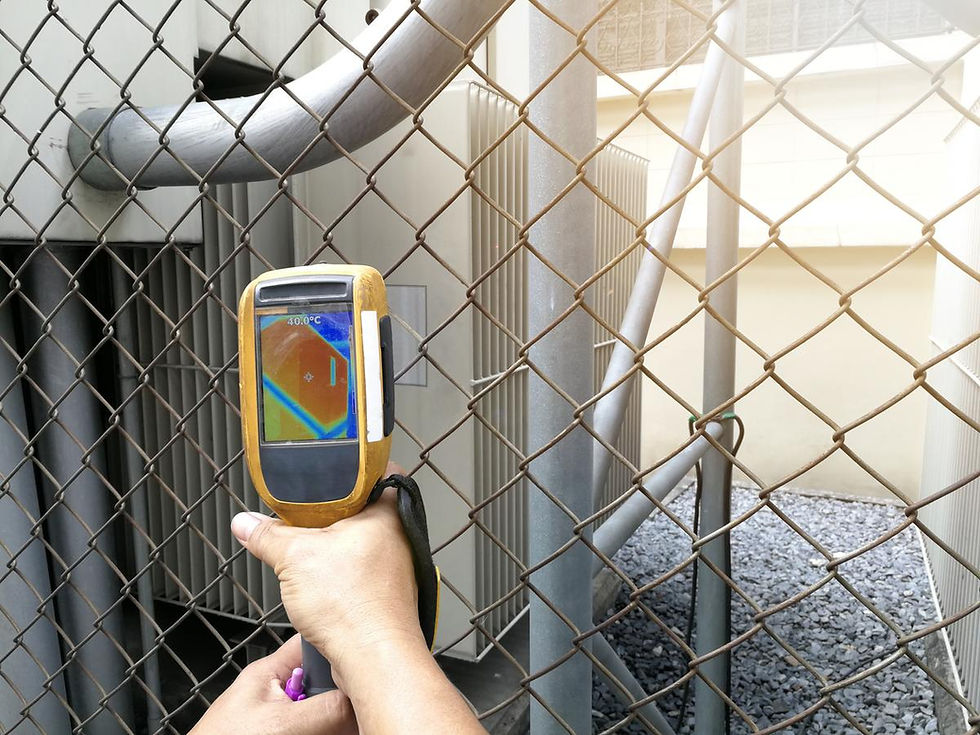
What is Thermographic Inspection?
Thermographic inspection, also known as thermal imaging or infrared inspection, is a non-contact technique that utilizes infrared cameras to detect and visualize temperature variations on the surface of objects and structures. It works on the principle that all objects emit infrared radiation in proportion to their temperature. By capturing these temperature patterns, thermographic cameras can reveal hidden anomalies and defects that are often invisible to the naked eye.
Applications of Thermographic Inspection
Electrical Systems:
Thermographic inspection is widely used in electrical systems maintenance. It can identify overheating components such as loose connections, faulty circuit breakers, and damaged electrical cables. Early detection of these issues can prevent electrical fires and costly downtime.
Mechanical Equipment:
Thermography is valuable for monitoring the condition of mechanical equipment like motors, pumps, and bearings. It can pinpoint areas of friction and stress, enabling predictive maintenance to prevent breakdowns and extend equipment lifespan.
Building Inspections:
In the construction industry, thermographic inspection can reveal insulation deficiencies, water leaks, and structural issues. It helps builders identify areas prone to energy loss and improve the overall energy efficiency of a building.
Roofing:
Detecting roof leaks early is essential to prevent water damage and structural deterioration. Thermographic inspection can identify moisture intrusion and insulation problems in roofing systems.
HVAC Systems:
Heating, ventilation, and air conditioning (HVAC) systems can benefit from thermographic inspections by revealing issues like clogged ducts, malfunctioning valves, and heat loss or gain.
Plumbing:
In plumbing, thermal imaging can identify hidden leaks and blockages, preventing water damage and mold growth.
Advantages of Thermographic Inspection:
Non-Destructive: Unlike traditional testing methods that may require disassembly or destruction, thermographic inspection is non-invasive and non-destructive, making it a valuable tool for preventative maintenance.
Early Detection: Thermography can identify problems at an early stage, allowing for timely repairs and preventing catastrophic failures.
Safety: It enables inspection of hazardous or hard-to-reach areas without risking human safety.
Cost-Efficiency: By preventing equipment breakdowns and reducing energy waste, thermographic inspection can result in significant cost savings over time.
Challenges and Considerations:
While thermographic inspection offers numerous benefits, it's essential to consider the following:
Training: Thermographic inspection requires skilled operators who understand the technology and its applications.
Environmental Factors: Weather conditions, temperature variations, and reflective surfaces can impact the accuracy of thermal imaging.
Regular Inspections: To maintain its effectiveness, thermographic inspections should be performed regularly as part of a comprehensive maintenance program.
Conclusion:
Thermographic inspection has revolutionized maintenance and inspection practices across various industries. Its ability to uncover hidden issues, prevent failures, and optimize efficiency makes it an invaluable tool for professionals seeking to ensure the safety, reliability, and longevity of their assets. As technology continues to advance, thermography is poised to play an even more significant role in predictive maintenance and quality control. For more information on property snagging please contact us here.